Surface + formulation = compatibility
Disinfecting surfaces is a cornerstone of good infection prevention.
That means surfaces in healthcare settings are frequently exposed to hospital-grade disinfectants. If the materials they're made from are incompatible with these disinfectants, it can lead to premature failure.
Surface material and disinfectant formulation are two of the most important factors affecting material compatibility.
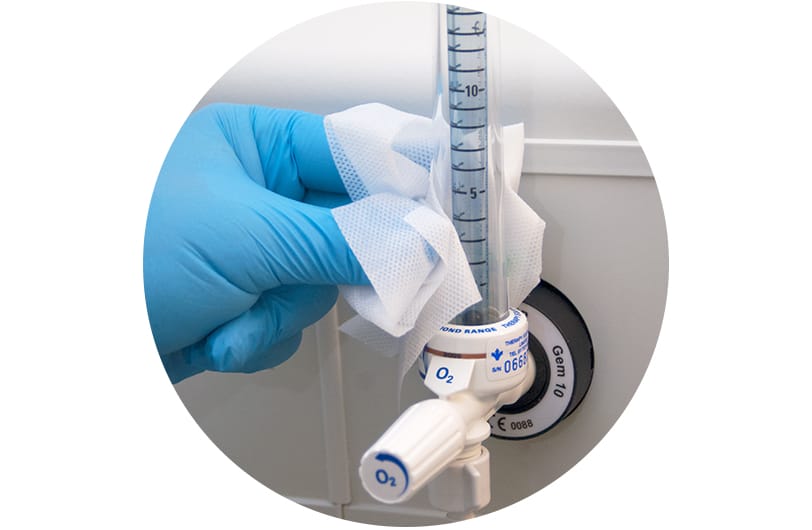
Surfaces
'Plastics' and 'polymers' are umbrella terms for hundreds of different chemical structures. Device manufacturers choose raw materials based on physical properties (differing strength, flexibility or thermal resistance), commercial availability or cost of production. Materials used in healthcare must consider an additional factor: resistance to disinfectants.
How does it work?
Healthcare equipment must be disinfected regularly for patient safety. Manufacturers should select materials able to withstand repeated exposure to disinfectants.
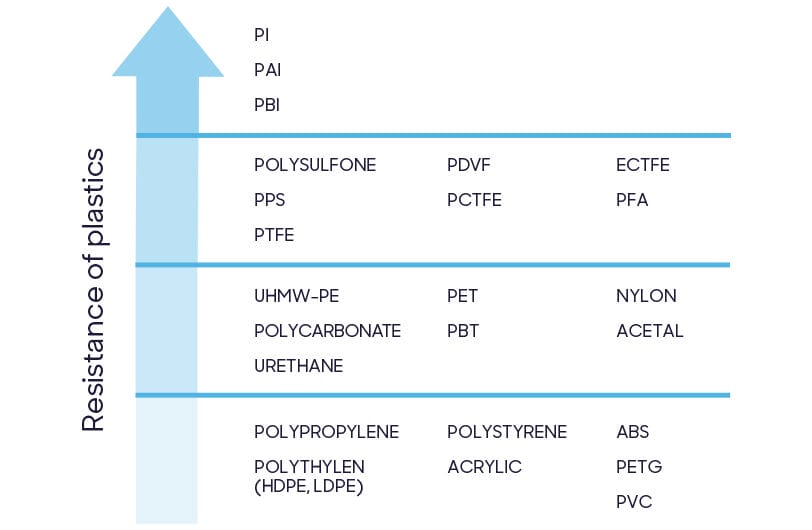
Formulation
Disinfectant products contain a 'formulation.' This is a mix of biocides (active ingredients that kill microbes), solvents and other additives (improving anything from stability to odour). Each one of these ingredients must be carefully selected to balance antimicrobial efficacy with material compatibility. If not, this can lead to 'environmental stress cracking'.
The problem
Environmental stress cracking is the premature cracking and embrittlement of plastic through two simultaneous actions: stress and contact with specific fluids. In cases of material incompatibility, active ingredients, solvents and additives found in disinfectants diffuse into the surface of plastic.
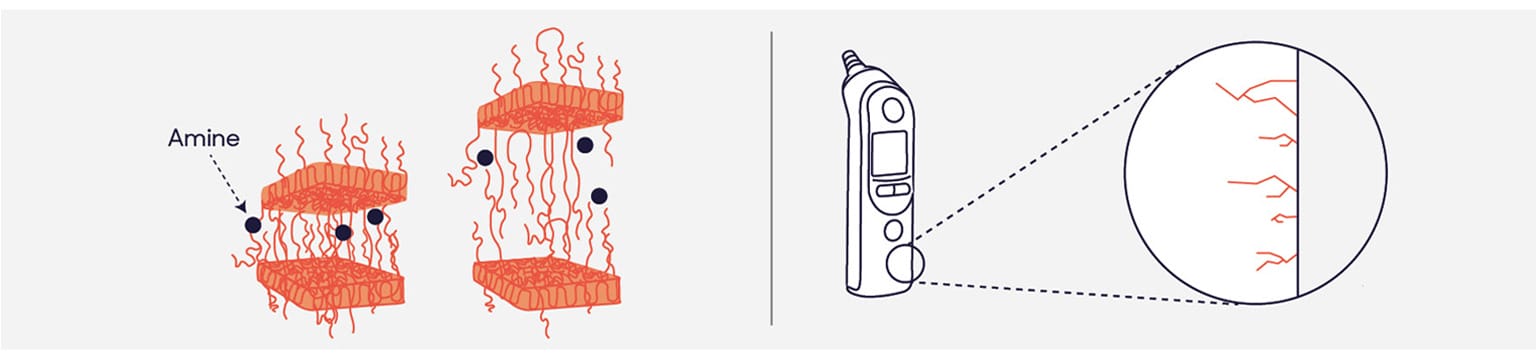
Exposure of susceptible materials to incompatible disinfectants causes the structure of polymers to change and detangle. This makes the plastic weaker and it becomes prematurely brittle.
When combined with stress, fine cracks form. Each formulation has varying compatibility with different surfaces. Amines, for example, are particularly aggressive to rubbers and plastics.

Continued exposure of susceptible surface materials to incompatible disinfectants causes cracks to rupture and deepen.
Cracks lead to premature failure of equipment and make surfaces harder to disinfect: providing a reservoir for pathogens.
The solution
Preventing material incompatibility takes a bilateral approach. Working together:
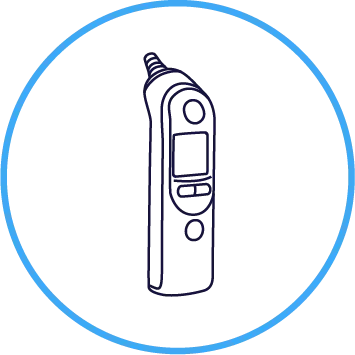
SURFACE AND DEVICE MANUFACTURERS NEED TO SELECT MORE DURABLE MATERIALS
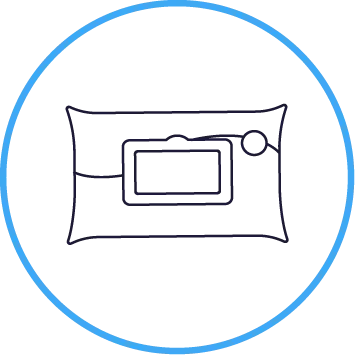
DISINFECTANT MANUFACTURERS NEED TO CREATE MORE SURFACE-FRIENDLY FORMULATIONS
Latest
Embracing sustainability and cost savings: The journey of Clinell Indicator Notes to paper-based solutions
At GAMA Healthcare, we’ve always prided ourselves on being at…
Introducing HEXI HUB: A seamless transition in our product line
We’re pleased to announce an update to our product offering…
Innovative solutions for tackling Carbapenemase-producing Enterobacteriaceae (CPE) at King’s College Hospitals
King’s College Hospital NHS Foundation Trust, one of London’s largest…
Gloves Off: reducing unnecessary plastic waste during environmental cleaning and disinfection
In this blog, Dr Phil Norville discusses the momentum-gaining ‘Gloves…
Gloves Off: Navigating SDS sheets and skin safety claims in environmental decontamination products
In this blog, James Clarke (Head of R&D, Science &…
Help reduce staff sickness and improve air ventilation with Rediair
As the winter season approaches, concerns over staff sickness and…
Moments that Matter: celebrating the fundamentals of infection prevention
To celebrate the fundamentals of infection prevention, we’re exploring the…
Tackling surface contamination is key to controlling Candida auris
Candida auris is a key emerging threat to healthcare facilities…
Save money on air purification with Rediair: A cost-effective solution to expensive alternatives
A comparative evaluation of three different stand-alone HEPA-based air systems…
New study links 2-in-1 wipes with reduced in-hospital mortality
In today’s blog, we’ll be discussing a new publication from…